Professional and high-quality metal alloys, ceramic products and concrete additives | RBOSCHCO
PRODUCT PARAMETERS
Description
Overview of Metal Alloy Titanium Rod for 3D Printing Powder
Steel Alloy Titanium Rod, mainly made for the manufacturing of 3D printing powder, is an innovative product in the additive production sector. This pole made up of titanium alloy, supplies remarkable mechanical residential or commercial properties and outstanding chemical resistance, making it an excellent selection for developing high-grade 3D-printed components. Its distinct structure enables specific control over the powder’s grain dimension and circulation, guaranteeing smooth and precise printing processes.

(Metal Alloy Titanium Rod For Making 3D Printing Powder)
Characteristics of Metal Alloy Titanium Rod
Superb Stamina and Longevity: This pole’s titanium alloy construction ensures phenomenal stamina and toughness, making it possible for the ultimately 3D-published components to have exceptionally high resistance to damage.
High Chemical Resistance: This product is immune to a variety of chemicals, ensuring security and toughness even in severe atmospheres.
Outstanding Toughness and Longevity: This pole’s titanium alloy structure makes certain phenomenal toughness and resilience, making it possible for the last 3D-printed components to be exceptionally immune to deterioration. High Chemical Resistance: This product is immune to a wide array of chemicals, making certain security and toughness also in extreme atmospheres.
Eco-Friendly: The use of titanium alloy in 3D printing powder promotes sustainability as it is recyclable and has a low environmental impact.
Parameter table of Metal Alloy Titanium Rod for 3D Printing Powder
Metal Alloy Titanium Rod For Making 3D Printing Powder Properties | |
Other Names | Titanium rod |
CAS No. | N/A |
Compound Formula | Ti |
Molecular Weight | N/A |
Appearance | N/A |
Melting Point | N/A |
Solubility in water | N/A |
Density | N/A |
Purity | N/A |
Size | customized |
Boling point | N/A |
Specific Heat | N/A |
Thermal Conductivity | N/A |
Thermal Expansion | N/A |
Young’s Modulus | N/A |
Exact Mass | N/A |
Monoisotopic Mass | N/A |
Metal Alloy Titanium Rod For Making 3D Printing Powder Health & Safety Information | |
Safety Warning | N/A |
Hazard Statements | N/A |
Flashing point | N/A |
Hazard Codes | N/A |
Risk Codes | N/A |
Safety Statements | N/A |
RTECS Number | N/A |
Transport Information | N/A |
WGK Germany | N/A |
Application of Metal Alloy Titanium Rod
Aerospace Market: The high stamina and light-weight nature of titanium alloy components make them excellent for usage in airplane and spacecraft elements.
Clinical Applications: Titanium alloy’s biocompatibility and deterioration resistance enable it to be utilized in implants and medical tools.
Automotive Industry: Titanium alloy parts can enhance the performance and durability of vehicles, especially in high-stress areas.
Consumer Products: From jewelry to household items, titanium alloy is a popular choice due to its aesthetic appeal and durability.
Research and Development: Its unique properties allow researchers to explore new design possibilities and applications in various fields.

Aerospace Industry

Medical Applications

Automotive Industry

Consumer Products

Research and Development
Production Method of Metal Alloy Titanium Rod for 3D Printing Powder
- Plasma Rotating Electrode Process (PREP): A titanium alloy rod is used as a consumable electrode. The electrode rotates at high speed while being heated and melted by a plasma arc. The molten metal is ejected by centrifugal force and atomized by an inert atmosphere, then condensed into spherical powder particles on the inner wall of the cold chamber. The powder has high sphericity, low oxygen content and narrow particle size distribution. Still, the yield of fine powder is low.
- Plasma Atomization (PA): A plasma jet melts titanium wire or rod to form powder with high sphericity. Its fine powder yield is more than twice that of PREP, but the equipment cost and energy consumption are high. PA is suitable for precision processes such as Selective Laser Melting (SLM), especially in the medical implant field.
- Gas Atomization (GA):High-speed gas flow breaks up the liquid metal stream, which then solidifies rapidly to form powder. GA has the advantages of low cost and high production efficiency, but the powder has high porosity and oxygen content and needs post-treatment. It is still the mainstream industrial powder-making technology at present.
- Hydrogenation-Dehydrogenation Method: The titanium material first undergoes surface purification treatment, then is hydrogenated to form brittle titanium hydride, which is crushed and sieved. After that, hydrogen is removed under high-temperature and vacuum conditions to obtain titanium powder. This method is low-cost and straightforward, but the powder sphericity and oxygen content need to be improved.
Company Profile
RBOSCHCO is a trusted global chemical material supplier & manufacturer with over 12-year-experience in providing super high-quality chemicals and nanomaterials, including boride powder, nitride powder, graphite powder, sulfide powder, 3D printing powder, etc.
The company has a professional technical department and Quality Supervision Department, a well-equipped laboratory, and equipped with advanced testing equipment and after-sales customer service center.
If you are looking for high-quality Metal Alloy Titanium Rod, please feel free to contact us or click on the needed products to send an inquiry.

Storage Condition of Metal Alloy Titanium Rod for 3D Printing Powder
Ecological Demands: The storage space setting ought to be completely dry and tidy, with a loved one moisture ideally listed below 40% to avoid powder cluster and oxidation. The temperature level ought to be preserved at 15 – 25 ° C to prevent thermal impacts on the powder’s residential or commercial properties.
Packaging Demands: The powder should be stored in vacuum-sealed or inert gas-filled packaging, such as argon or nitrogen, to isolate it from air and moisture. The packaging material should be antistatic to prevent the electrostatic adsorption of powder particles.
Location Selection: Store it in a well-ventilated space, away from direct sunlight and heat sources, and avoid contact with corrosive substances and strong magnetic fields.
Payment Term
L/C, T/T, Western Union, Paypal, Credit Card etc.

Shipment Term
By sea, by air, by express, as customers request.
5 FAQs of Metal Alloy Titanium Rod for 3D Printing Powder
Q1:
What are the advantages of using Metal Alloy Titanium Rod for 3D printing powder?
Re: The main benefits of using Steel Alloy Titanium Pole for 3D printing powder include its outstanding stamina and toughness, high chemical resistance, accuracy grain control, simple handling, and eco-friendliness. These functions guarantee high-grade published get rid of premium efficiency and longevity.
Q2:
Is the titanium alloy used in the rod recyclable?
Re: Yes, the titanium alloy utilized in the pole is recyclable, which makes it an eco-friendly selection for 3D printing powder manufacturing. This adds to sustainability and lowers waste in the production procedure.
Q3:
Can the Metal Alloy Titanium Rod be used in the medical industry?
Re: Definitely, the biocompatibility and rust resistance of titanium alloy make it appropriate for usage in the clinical sector. It can be utilized to develop implants, medical tools, and various other clinical gadgets that call for high toughness and security.
Q4:
How does the rod ensure precision grain control in the 3D printing powder?
Re: The structure and production procedure of the Steel Alloy Titanium Pole are developed to make certain accuracy grain control in the resulting 3D printing powder. This permits the manufacturing of powders with constant and consistent grain dimensions, making it possible for high-resolution and smooth printing.
Q5:
Is the Metal Alloy Titanium Rod suitable for large-scale production?
Re: Yes, the Steel Alloy Titanium Pole is developed for effective and simple handling, making it ideal for large manufacturing of 3D printing powder. Its reputable efficiency and scalability enable economical production of premium published components.
REQUEST A QUOTE
RELATED PRODUCTS
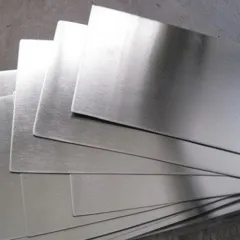
High Quality Titanium Sheet Factory Price Mirror Black Ti Titanium Plate/Sheet
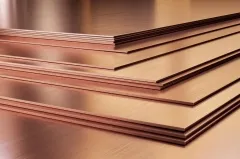
Excellent Conductivity 99.99% Pure Copper Flat Sheet Plate Price Per KG
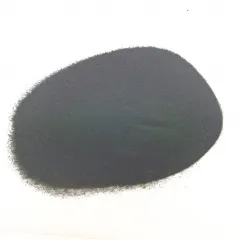
Customized Aluminum Silicon Powder AlSi Alloy Powder
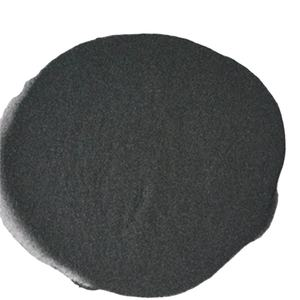
Pre-alloyed Iron Copper FeCu Powder
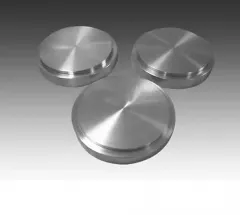
Titanium Sputtering Target/ Pure Titanium Target /alloy Titanium Target for Vacuum Coating
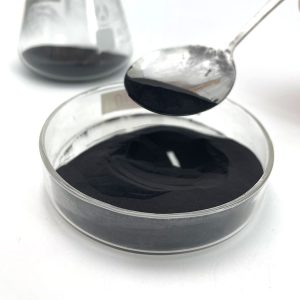