Professional and high-quality metal alloys, ceramic products and concrete additives | RBOSCHCO
Metal Alloy
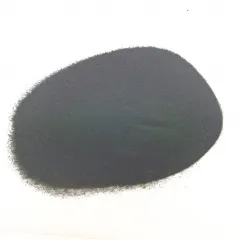
Customized Aluminum Silicon Powder AlSi Alloy Powder
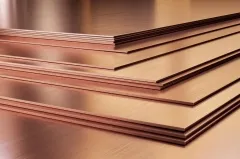
Excellent Conductivity 99.99% Pure Copper Flat Sheet Plate Price Per KG
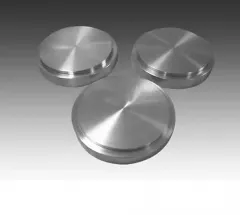
Titanium Sputtering Target/ Pure Titanium Target /alloy Titanium Target for Vacuum Coating
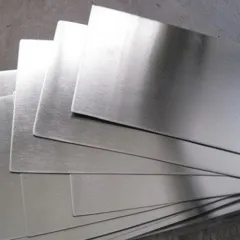
High Quality Titanium Sheet Factory Price Mirror Black Ti Titanium Plate/Sheet
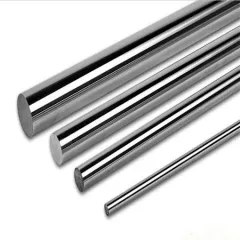
Factory Outlet High Purity Titanium Rod in Best Price
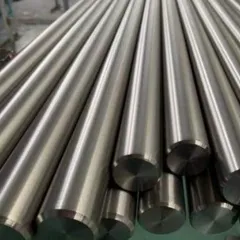
Metal Alloy High Temperature Inconel718 Alloy Rod
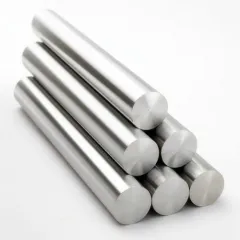
Metal Alloy High Temperature Inconel625 Alloy Rod
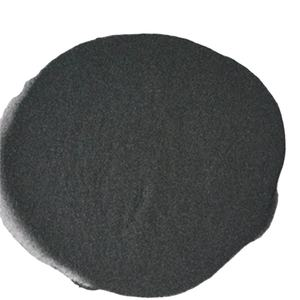
Pre-alloyed Iron Copper FeCu Powder
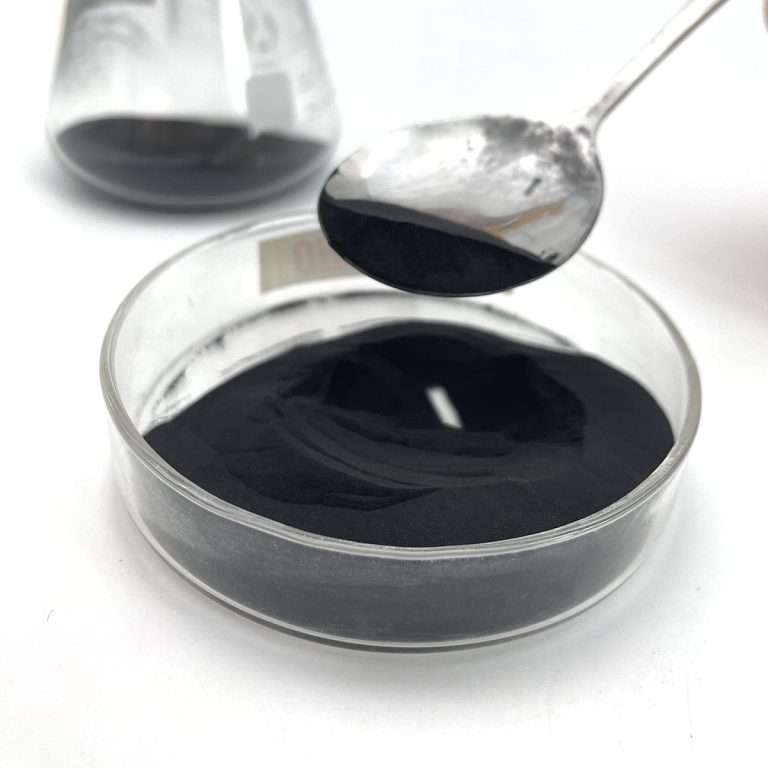
Copper Nickel Cu-Ni Alloy Powder
Overview of Metal Alloys
Metal alloys, a blend of metals and other elements, offer superior properties to pure metals. They have been a cornerstone of engineering and manufacturing for centuries due to their strength, flexibility, corrosion resistance, and cost-effectiveness. Alloys can be customized to satisfy details demands, making them crucial in numerous applications.
Specifications of Metal Alloys
Parameter | Description |
---|---|
Alloy Composition | Depends on the product |
CAS Number | Not typically provided for alloys |
Grade/Standard Compliance | Depends on the product |
Purity (%) | Depends on the product |
Particle Size Distribution (PSD) | Range: 15-45 µm |
Morphology | Spherical |
Surface Area (m²/g) | Depends on the product |
Bulk Density (g/cm³) | Depends on the product |
Tap Density (g/cm³) | Depends on the product |
Flowability | Depends on the product |
Oxygen Content (%) | Depends on the product |
Nitrogen Content (%) | Depends on the product |
Carbon Content (%) | Depends on the product |
Moisture Content (%) | Depends on the product |
pH Value | Depends on the product |
Electrical Conductivity (S/m) | Depends on the product |
Melting Point (°C) | Depends on the product |
Boiling Point (°C) | Depends on the product |
Thermal Conductivity (W/m·K) | Depends on the product |
Coefficient of Thermal Expansion (CTE) (1/°C) | Depends on the product |
Magnetic Properties | Paramagnetic |
Chemical Reactivity | Generally inert, but reactive with halogens at high temperatures |
Mechanical Properties | Depends on the product |
Corrosion Resistance | Excellent in oxidizing environments; susceptible to crevice corrosion |
Safety Data | Refer to the Material Safety Data Sheet (MSDS) |
Storage Conditions | Store in a cool, dry place, away from moisture and contaminants |
Packaging | Typically supplied in sealed containers or vacuum-sealed bags |
Application Notes | Ideal for additive manufacturing, especially for parts requiring high strength-to-weight ratio and biocompatibility |
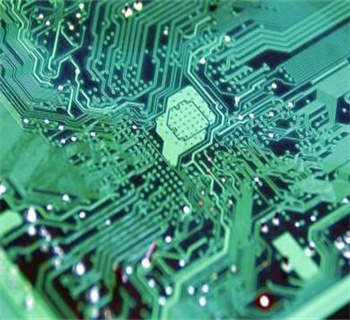
Features and benefits of metal alloy powders
Metal alloy powders have the following distinctive features and benefits that make them an integral part of modern industry:
High designability:
Composition ratios can be adjusted according to specific needs to optimize the mechanical, physical and chemical properties of the material to meet the requirements of different application scenarios.
Excellent mechanical properties:
High strength, high hardness, good toughness, suitable for working environments with high loads.
Excellent corrosion and oxidation resistance:
Especially titanium-based and nickel-based alloy powders can maintain stability in harsh environments and extend service life.
Good processing performance:
Powders are easy to mold, and can be made into complex shaped parts through a variety of processes (e.g., pressing, sintering, injection molding, etc.), reducing subsequent processing steps.
Uniform and consistent quality:
Modern production process ensures uniform size distribution of powder particles and stable chemical composition, thus ensuring consistent quality of the final product.
Environmentally friendly and energy efficient:
Compared to traditional casting or forging methods, the use of metal alloy powders reduces energy consumption and minimizes waste generation, in line with the concept of green manufacturing.
Multifunctionality:
The same alloy powder may simultaneously have a variety of functional properties, such as both good electrical conductivity and a certain degree of magnetism, broadening its scope of application.
Cost-effective:
For some materials that are difficult to process through traditional methods, the use of metal alloy powder technology can simplify the process, reduce costs and improve production efficiency.
Applications of Metal Alloy Powders
Metal alloy powders have a wide range of applications in several fields due to their unique physical and chemical properties. Below are a few of the main applications:
Additive manufacturing (3D printing):
Aerospace: for the manufacture of lightweight, high-strength components, such as engine parts, structural components, etc.
Medical industry: customized implants (e.g. hip and knee prostheses), dental restorations, etc.
Thermal Spraying:
Applied to surface treatment to enhance the wear resistance, corrosion resistance and thermal stability of materials, commonly used in automotive engine parts, molds, etc.
Powder metallurgy:
Manufacturing of complex shaped mechanical parts, such as gears, bearings, etc., suitable for mass production and cost-effective occasions.
Injection Molding:
Mixing metal powder with binder for injection molding, suitable for manufacturing small precision parts, such as electronic component housings, watch parts, etc.
Welding and Repair:
Used for automatic or manual welding and repair of old equipment, it can provide good metallurgical bonding and mechanical properties.
Cemented Carbide Manufacturing:
To produce cutting tools, drills and other products that require high hardness and wear resistance.
Chemical Industry:
Certain metal alloy powders are used as catalysts or reaction media to participate in chemical synthesis processes.
Electronic industry:
Manufacture of high-performance magnetic materials, conductive materials and shielding materials.
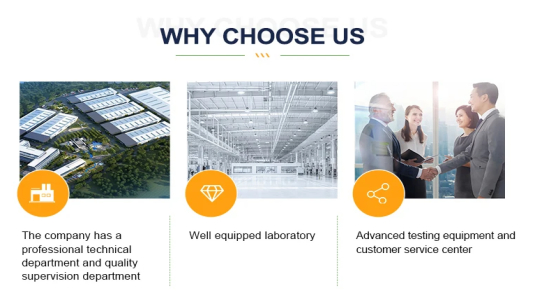
Company Profile
Rboschco.com is a trusted global chemical material supplier & manufacturer with over 12-year-experience in providing super high-quality chemicals and nanomaterials, including boride powder, nitride powder, graphite powder, sulfide powder, 3D printing powder, etc.
The company has a professional technical department and Quality Supervision Department, a well-equipped laboratory, and equipped with advanced testing equipment and after-sales customer service center.
If you are looking for high-quality Metal alloys, please feel free to contact us or click on the needed products to send an inquiry.
Payment Term
L/C, T/T, Western Union, Paypal, Credit Card etc.
Shipment Term
By sea, by air, by express, as customers request.
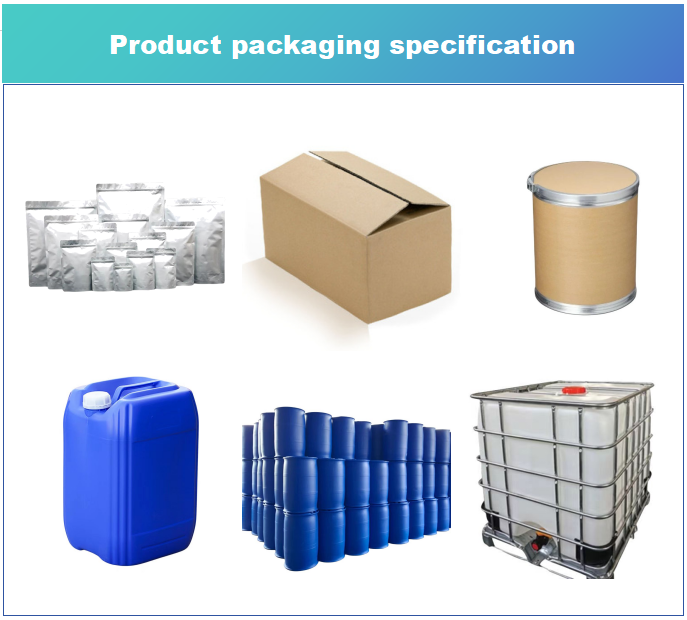
FAQ
Q1:
How do I select the right metal alloy powder for a particular application?
Re: Application requirements: Determine the required mechanical properties (e.g. strength, toughness), physical properties (e.g. electrical conductivity, coefficient of thermal expansion) and chemical stability.
Manufacturing process: Different manufacturing techniques have different requirements for powders, e.g. Laser Powder Bed Fusion (LPBF) requires powders with good flowability and sphericity.
Cost-effectiveness: Assess the balance between material cost, processing cost and market value of the final product.
Standards compliance: Ensure that the selected material complies with relevant international standards (e.g. ASTM, ISO) for quality and safety.
Q2:
What do I need to know about the safe handling and storage of metal alloy powders?
Re: Good ventilation: The work area should be well ventilated to avoid dust accumulation.
Protective equipment: Operators should wear appropriate personal protective equipment (PPE) such as masks, gloves and goggles.
Moisture and oxidation prevention: Many metal powders tend to absorb moisture or oxidize easily, so they should be stored in dry, sealed containers.
Fire precautions: Keep away from sources of ignition and have appropriate fire extinguishing equipment, such as dry powder fire extinguishers.
Follow MSDS: Strictly follow the guidelines in the Material Safety Data Sheet (MSDS).
Q3:
Are metal alloys recyclable?
Re: Yes, metal alloys are generally recyclable. Depending on the composition, they can be melted down and reprocessed into new alloys or pure metals. Recycling metal alloys reduces waste, conserves resources, and reduces energy consumption compared to producing new alloys from virgin materials.
Q4:
What are the disadvantages of using metal alloys?
Re: While metal alloys offer many advantages, they also have disadvantages. One major drawback is their susceptibility to corrosion, especially in harsh environments. Additionally, some alloys may be more expensive than pure metals due to their specialized composition and production processes. Furthermore, certain alloys may not be suitable for high-temperature applications or in environments with extreme chemical exposure.
Q5:
How do metal alloys affect the environment?
Re: The production and disposal of metal alloys can impact the environment. The mining and smelting processes used to produce alloys can release harmful emissions and waste. Additionally, if alloys are not recycled properly, they can end up in landfills, causing soil and water pollution. However, many industries are moving towards more sustainable production methods and recycling practices to minimize the environmental impact of metal alloys.