Professional and high-quality metal alloys, ceramic products and concrete additives | RBOSCHCO
PRODUCT PARAMETERS
Description
Overview Of 3D Printing Nickel Alloy Inconel 718 Powder
Inconel 718 powder is mainly composed of nickel (Ni), chromium (Cr), and iron (Fe), as well as small amounts of other elements such as niobium (Nb), molybdenum (Mo), and titanium (Ti). This nickel alloy has good corrosion resistance, high-temperature strength, oxidation resistance, creep resistance, and fatigue strength.
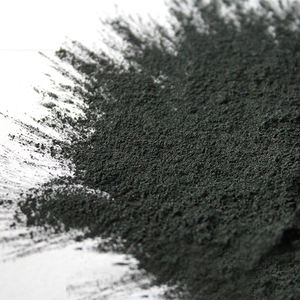
(3D Printing Nickel Alloy Inconel 718 Powder)
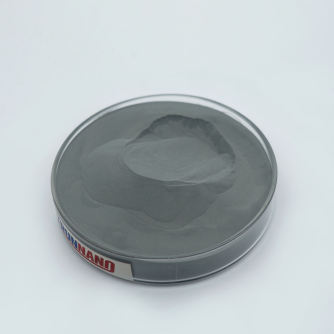
3D Printing Alloy Spherical Tungsten Nickel Iron Alloy Powder
Features of 3D Printing Nickel Alloy Inconel 718 Powder
3D printing nickel alloy Inconel 718 powder offers several key features. It has a high nickel content, along with chromium, iron, niobium, and other alloying elements. This composition endows it with excellent high-temperature strength, allowing printed parts to maintain structural integrity up to around 650°C. The powder has good flowability due to its spherical particle shape, ensuring smooth delivery in 3D printers for consistent layer deposition. It shows remarkable corrosion resistance in various media, including saltwater and harsh chemicals. Inconel 718 powder likewise makes it possible for the manufacturing to get rid of high tiredness resistance, which is critical for applications like aerospace parts that withstand cyclic loading. After 3D printing, components can be heat-treated to enhance their mechanical residential or commercial properties additionally, attaining high firmness and tensile toughness while keeping ductility.
Parameter table of 3D Printing Nickel Alloy Inconel 718 Powder
Nickel Alloy IN718 Powder Properties | |
Other Names | IN718, Inconel-718 powder, Inconel 718 Powder |
CAS No. | N/A |
Compound Formula | Ni/Fe/Cr |
Molecular Weight | N/A |
Appearance | Gray to black powder |
Melting Point | 1370-1430 °C |
Solubility in water | N/A |
Density | 8.192 g/cm3 |
Purity | N/A |
Particle Size | 15-45μm, 15-53μm, 53-120μm, 53-150μm |
Boling point | N/A |
Specific Heat | N/A |
Thermal Conductivity | 6.5 W/m·K |
Thermal Expansion | N/A |
Young’s Modulus | N/A |
Exact Mass | N/A |
Monoisotopic Mass | N/A |
Nickel Alloy IN718 Powder Health & Safety Information | |
Safety Warning | Danger |
Hazard Statements | H317-H351-H372 |
Flashing point | N/A |
Hazard Codes | Xn |
Risk Codes | N/A |
Safety Statements | N/A |
RTECS Number | N/A |
Transport Information | NONH for all modes of transport |
WGK Germany | N/A |
Applications Of 3D Printing Nickel Alloy Inconel 718 Powder
3D printing Nickel Alloy Inconel 718 Powder has a large range of applications in various fields, mainly including the following:
Aerospace field: Inconel 718 powder has essential applications in the aerospace field. It is widely used to manufacture key components of jet engines, such as turbine blades, combustion chambers, gas turbines, burners, and other elements of aircraft engines. Due to their excellent high-temperature performance and corrosion resistance, these components can operate stably under extreme working conditions.
Energy sector: Inconel 718 powder is used to produce key components such as nuclear fuel tanks, turbine blades, and steam generators in nuclear power plants. It is also used to manufacture components such as burners and boiler pipelines in thermal power plants.
Petrochemical industry: Due to its excellent corrosion resistance and high-temperature stability, Inconel 718 powder has also been widely used in the petrochemical industry. It manufactures components in petrochemical equipment and pipeline systems, such as catalyst carriers, distillation towers, oil well equipment, and submarine pipelines.
Automotive Industry: Inconel 718 powder is used to manufacture high-temperature engine components such as turbine blades and exhaust systems. Its high-temperature strength and corrosion resistance can meet the engine’s requirements in high-temperature and corrosive environments.

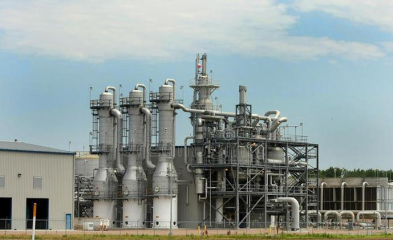
Applications of 3D Printing Nickel Alloy Inconel 718 Powder
Production Method of 3D Printing Nickel Alloy Inconel 718 Powder
The production of 3D – printing nickel alloy Inconel 718 powder mainly involves the following methods:
Gas Atomization First, high-purity raw materials of nickel, chromium, iron, niobium, and other alloying elements are precisely weighed according to the Inconel 718 composition. These are placed in an induction furnace under an inert argon atmosphere. The stove heats the materials to around 1500 – 1600 °C until they entirely melt and form a homogeneous molten alloy. The molten alloy is then poured through a small nozzle at a controlled rate. High-pressure argon gas is sprayed onto the molten stream, shattering it into tiny droplets. Due to surface tension, these droplets form spherical shapes. As they fall through the gas-filled chamber, they rapidly cool and solidify into powder. The powder is collected at the bottom and later sieved to obtain the desired particle size distribution.
Plasma Rotating Electrode Process (PREP) A consumable electrode made of Inconel 718 is prepared. This electrode is rotated at a very high speed in a vacuum or inert gas environment. A plasma arc is generated at the end of the rotating electrode, melting the tip. The centrifugal force from the high-speed rotation causes the molten metal to be ejected as fine droplets. These droplets solidify in the surrounding environment to form a spherical powder. PREP can produce a powder with low oxygen content and reasonable particle size control, suitable for high-performance 3D printing applications.
Company Profile
RBOSCHCO is a trusted global chemical material supplier & manufacturer with over 12-year-experience in providing super high-quality chemicals and nanomaterials, including boride powder, nitride powder, graphite powder, sulfide powder, 3D printing powder, etc.The company has a professional technical department and Quality Supervision Department, a well-equipped laboratory, and equipped with advanced testing equipment and after-sales customer service center.If you are looking for high-quality 3D Printing Nickel Alloy Inconel 718 Powder, please feel free to contact us or click on the needed products to send an inquiry.
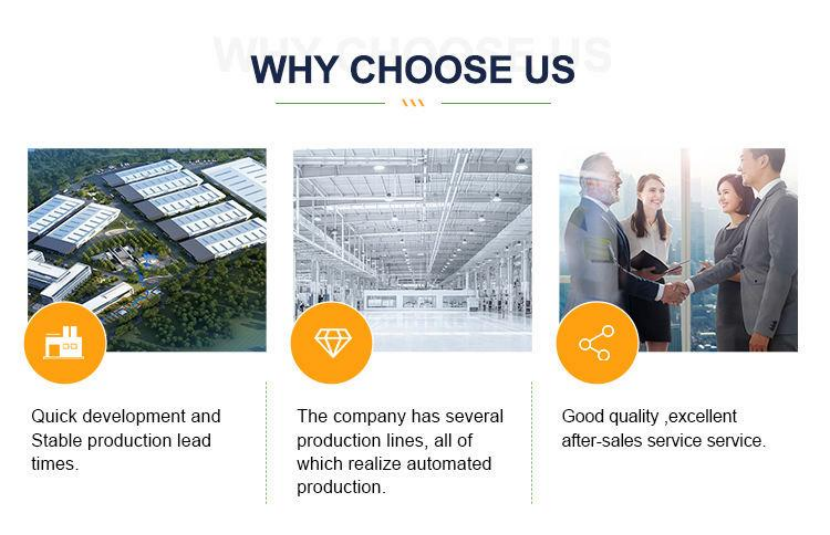
Storage Condition of 3D Printing Nickel Alloy Inconel 718 Powder
1) Store in a dry environment at room temperature.
2) Avoid damp and high temperature.
3) Use immediately after opening the inner packing bag.
Payment Term
L/C, T/T, Western Union, Paypal, Credit Card etc.
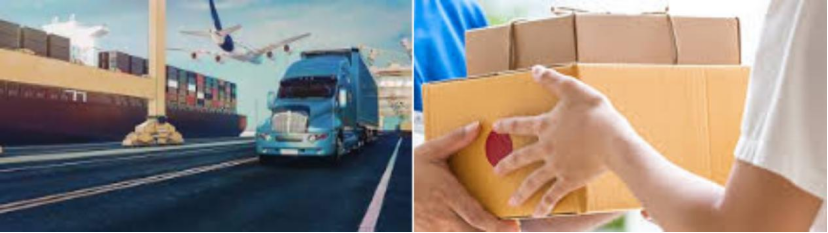
Shipment Term
By sea, by air, by express, as customers request.
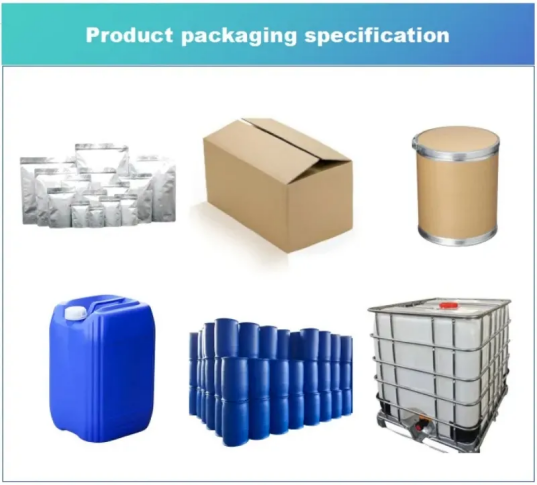
5 FAQs of 3D Printing Nickel Alloy Inconel 718 Powder
Q1
What is Inconel 718 powder?
Answer: Inconel 718 powder is a nickel-based high-temperature alloy powder composed of nickel, chromium, iron, and other alloying elements such as niobium, molybdenum, titanium, etc. It has excellent high-temperature strength, corrosion, oxidation, and creep resistance.
Q2
Why choose 3D printing Inconel 718 powder?
Answer: 3D printing Inconel 718 powder can manufacture complex shaped components, reduce material waste, and improve production efficiency. In addition, the high-temperature performance of this alloy makes it an ideal choice for high-temperature components in fields such as aviation, energy, and petrochemicals.
Q3
What is the 3D printing process for Inconel 718 powder?
Answer: 3D printing of Inconel 718 powder typically uses selective laser melting (SLM) or electron beam melting (EBM) technology. The powder is stacked layer by layer and melted by the energy of a laser or electron beam, followed by cooling and solidification to form the required components.
Q4
What are the application areas of Inconel 718 powder-printed components?
Answer: Inconel 718 powder-printed components, such as turbine engine blades, combustion chambers, and gas turbines, are widely used in the aerospace industry. In addition, they are also used in nuclear power plants and thermal power plants in the energy sector, as well as in petrochemical equipment and engine components in the automotive industry and other fields.
Q5
What are the advantages of Inconel 718 powder-printed components?
Answer: The printed components have high-temperature strength, corrosion resistance, good mechanical properties, and precise dimensions, which can meet the requirements of complex and harsh working environments. In addition, 3D printing technology can also achieve customization and rapid prototyping.
REQUEST A QUOTE
RELATED PRODUCTS
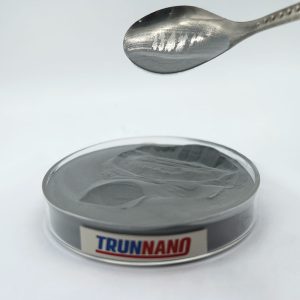
Aluminium Alloy AlSi10Mg Powder for 3D Printing Price Aluminium Alloy Powder AlSi10Mg Powder
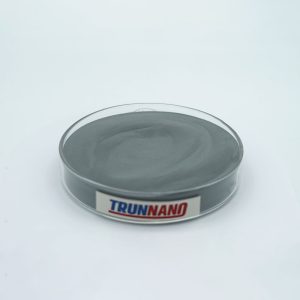
3D Printing Nickel Alloy Powder Inconel 738 Powder
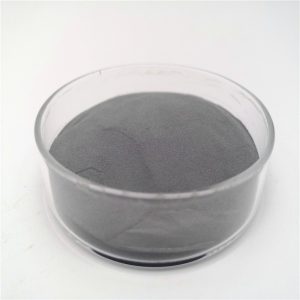
3D Printing Alloy CoCrW Powder
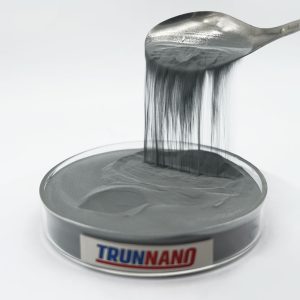
3D Printing Aluminum Based Alloy AlSi7Mg Powder
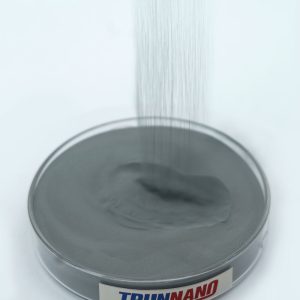
3D Printing Alloy Spherical Titanium Powder
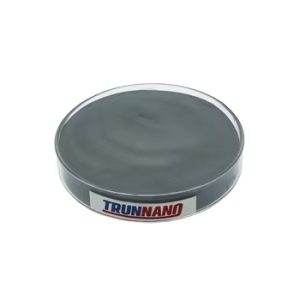