Professional and high-quality metal alloys, ceramic products and concrete additives | RBOSCHCO
PRODUCT PARAMETERS
Description
Introduction of Zirconia Bricks
Zirconia bricks are high-performance refractory materials made from zirconium oxide (ZrO₂) with excellent resistance to high temperatures, corrosion, and thermal shock. Zirconia is an advanced ceramic material stabilized (e.g., with the addition of yttrium oxide) to maintain stable physical and chemical properties under extreme environments. Zirconia bricks are widely used in high-temperature industrial furnaces, metallurgical equipment, chemical reactors, and other scenarios and are an indispensable key material in high-temperature processes.
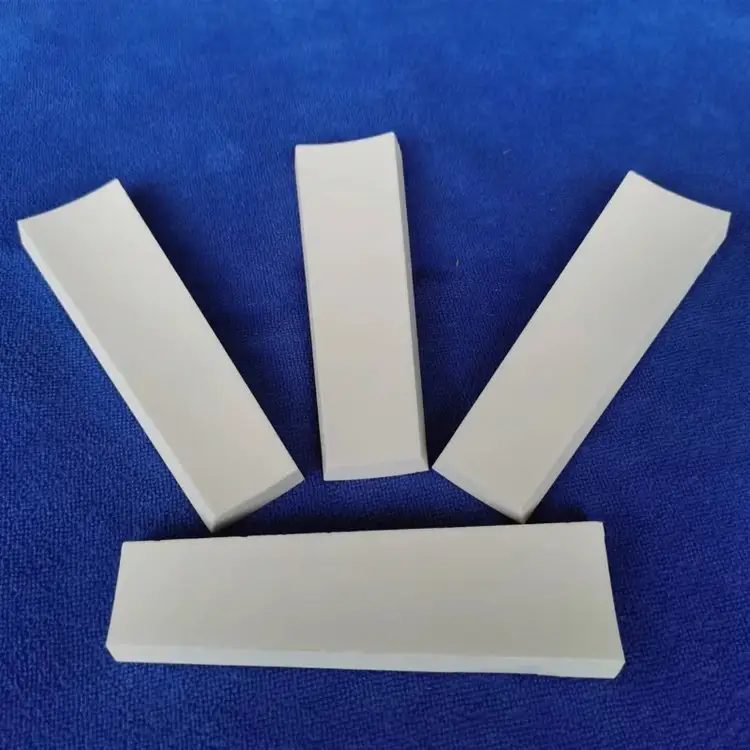
Features of Zirconia Bricks
High-temperature resistance: zirconia has a melting point of up to 2700°C and is capable of working stably in high-temperature environments above 1800°C for a long period of time.
Excellent thermal shock resistance: able to withstand rapid temperature changes, suitable for frequent heating and cooling conditions.
Chemical stability: excellent corrosion resistance to acids, alkalis, and molten metals, suitable for harsh chemical environments.
High mechanical strength: high hardness and toughness, able to withstand greater mechanical stress and wear.
Low thermal conductivity: good thermal insulation properties, reducing heat loss and improving energy efficiency.
Low contamination: no contamination of the molten material under high temperature environment, suitable for the preparation of high purity materials.
Oxidation resistance: It remains stable in a high-temperature oxidizing environment and is not easy to change chemically.
Parameters of Zirconia Bricks
Parameter | Description | Typical Values/Range |
Chemical Composition | Primary components | ZrO2 ≥ 92%, Stabilizers (Y2O3, MgO, CaO) |
Density | Mass per unit volume | 5.8 – 6.1 g/cm³ |
Apparent Porosity | Percentage of void space | ≤ 15% |
Refractoriness Under Load (RUL) | Temperature at which the brick deforms under load | > 1700°C |
Cold Crushing Strength (CCS) | Resistance to crushing at room temperature | 100 – 300 MPa |
Thermal Expansion Coefficient | Rate of expansion with temperature increase | 7 – 10 × 10⁻⁶ /°C |
Thermal Conductivity | Ability to conduct heat | Low, typically < 2.0 W/m·K at 1000°C |
Thermal Shock Resistance | Ability to withstand rapid temperature changes | Excellent |
Resistance to Slag Erosion | Resistance to erosion by molten slag | High |
Corrosion Resistance | Resistance to chemical attack | Excellent resistance to acids, alkalis, and molten metals |
Size and Shape | Dimensions and shapes available | Standard brick sizes, custom shapes available |
Surface Finish | Smoothness or roughness of the surface | Smooth finish, can be customized |
Phase Stability | Stability of zirconia phases at high temperatures | Tetragonal or cubic phase stabilized |
Applications of Zirconia Bricks
Metallurgical industry: used as lining material for high-temperature melting furnaces, electric arc furnaces, and induction furnaces; used as refractory material in the melting and purification process of rare metals and precious metals (such as platinum, gold, silver, etc.).
Glass and ceramic industry: used as lining materials for glass melting kilns and ceramic sintering furnaces, which are capable of withstanding high temperatures and chemical corrosion. They are also used as high-temperature-resistant container materials in the preparation of optical glass and special glass.
Chemical industry: used as lining materials for high-temperature reactors and corrosive media handling equipment; used as corrosion-resistant refractory materials in catalyst preparation and high-temperature catalytic reactions.
Energy and environmental protection field: used for high-temperature components of solid oxide fuel cell (SOFC); used as high-temperature and corrosion-resistant lining material in waste gas treatment and waste incinerator.
Electronics and semiconductor industry: used for high-temperature melting furnace lining of monocrystalline silicon, polycrystalline silicon, and other semiconductor materials; used as high-temperature reaction vessel materials in the preparation of electronic ceramic materials.
Aerospace and nuclear energy fields: used in high-temperature experimental equipment and heat protection materials, as well as refractory materials in high-temperature experiments and research of nuclear fuel and related materials.
Company Profile
RBOSCHCO is a trusted global chemical material supplier & manufacturer with over 12 years experience in providing super high-quality chemicals and Nanomaterials.
The company has a professional technical department and Quality Supervision Department, a well-equipped laboratory, and equipped with advanced testing equipment and after-sales customer service center.
If you are looking for high-quality Zirconia Bricks please feel free to contact us or click on the needed products to send an inquiry.
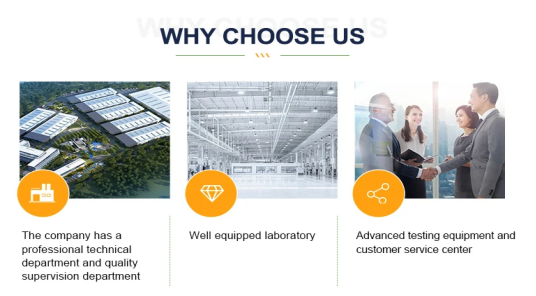
Payment Term
T/T, Western Union, Paypal, Credit Card etc.
Packing and Storage
The product is in powder form and should be stored in a cool, ventilated place. Avoid inhalation when using it and keep away from open flames, heat sources, etc.
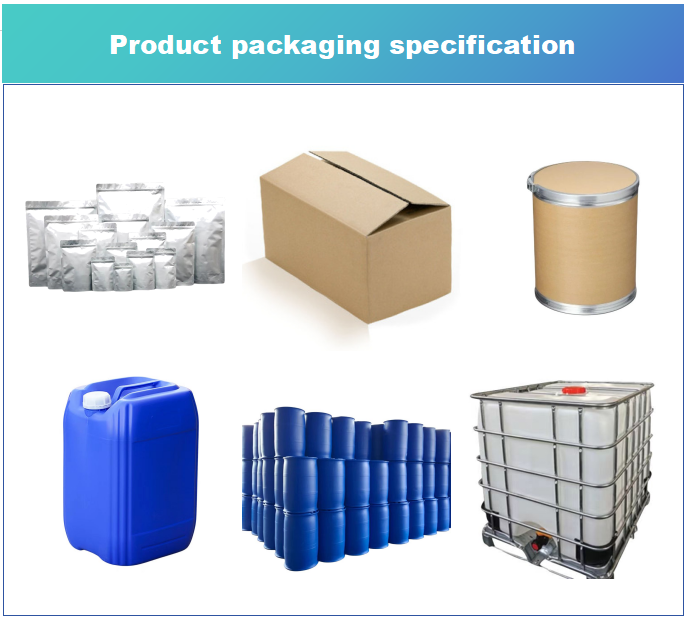
Shipment Term
By air, by sea, by express, as customers request.
FAQs of Zirconia Bricks
Question 1: What are the main application areas of zirconia bricks?
Answer: Zirconia bricks are mainly used in critical parts of high-temperature industrial equipment, such as ladles, converters, and continuous casting intermediate ladles in iron and steel mills, and flow holes, breast walls, and necks in glass melting kilns. They are also used in non-ferrous metal smelting, cracking furnaces in the petrochemical industry, and ceramic firing kilns in environments where they are subjected to extreme temperatures and chemical attacks. In addition, zirconia bricks are used as a protective material for internal components of nuclear reactors in some special cases.
Question 2: What are the advantages of zirconia bricks over other refractory materials?
Answer: Zirconia bricks have a higher melting point (up to 2700°C), better thermal shock resistance, higher wear resistance, and better chemical stability than conventional silica or aluminosilicate refractories. These properties allow zirconia bricks to perform consistently over long periods of time under more demanding operating conditions, reducing maintenance frequency and extending service life. In addition, their low thermal conductivity helps to reduce heat loss and improve energy efficiency.
Question 3: Are zirconia bricks susceptible to thermal shock?
Answer: Zirconia bricks are known for their excellent resistance to thermal shock and cope well with stress changes caused by rapid heating and cooling. This is due to the fact that zirconia materials absorb a large amount of energy as they undergo a phase change, accompanied by volume expansion, which relieves the internal stresses caused by sudden temperature changes. However, despite this, care needs to be taken to avoid extreme temperature fluctuations during design and use to ensure optimum performance.
QUESTION 4: How do I select the right zirconia brick for a particular application?
Answer: Selecting the right zirconia brick depends on the specific application conditions, including factors such as maximum service temperature, nature of the atmosphere, chemical environment, and expected mechanical loads. For applications at very high temperatures, a fully stabilized zirconia brick should be considered, while in the presence of a complex chemical attack, a partially stabilized zirconia (PSZ) or tetragonal phase zirconia (TZP) with good chemical inertness is required. Brick size, shape, and installation should also be evaluated to ensure compatibility with existing systems.
Question 5: Why is the thermal shock resistance of zirconia bricks important?
Answer: Thermal shock resistance of zirconia bricks is important for a number of reasons, including Adaptation to temperature changes. In high-temperature industrial equipment, where temperatures can change frequently, thermal shock resistance prevents the brick from cracking or being damaged. Extending service life: good thermal shock resistance reduces material fatigue and failure due to thermal stress, extending service life. Improved safety: avoiding equipment failures or production interruptions due to cracked bricks ensures process continuity and safety.
REQUEST A QUOTE
RELATED PRODUCTS
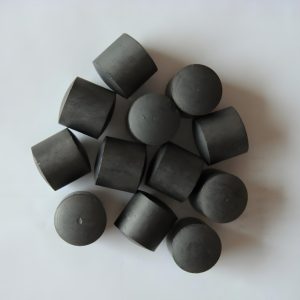
Fire and Corrosion Resistant Silicon Carbide Ceramic Grinding Balls
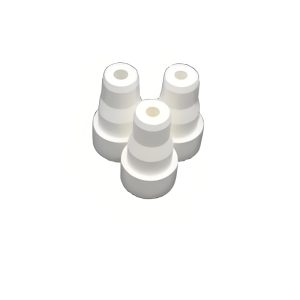
BN ceramic nozzle high purity ceramics boron nitride insulator nozzle
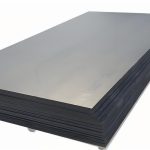
Refractory Ceramic Substrates Silicon Nitride Plates Si3N4

AlN High-temperature High-thermal Conductivity High-performance Aluminum Nitride Ceramic Tube
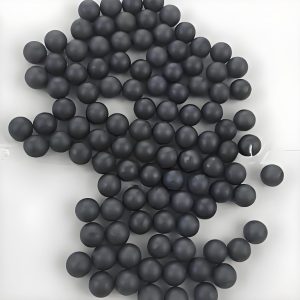
Grinding Media High Purity Boron Carbide B4C Grinding Balls
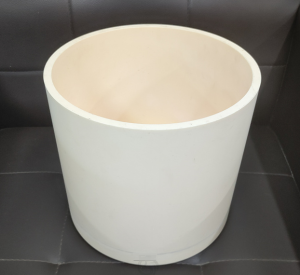