Professional and high-quality metal alloys, ceramic products and concrete additives | RBOSCHCO
PRODUCT PARAMETERS
Description
Overview of Alumina Porcelain Balls
High alumina ceramic spheres, likewise referred to as ceramic alumina balls, are high-performance products mostly composed of aluminum oxide (Al ₂ O ₃). With alumina content varying from 92% to 99.5%, these ceramic rounds are renowned for their superb solidity, put on resistance, and thermal stability. They are commonly made use of in a range of sectors, including grinding, milling, chemical processing, and petrochemical applications. High alumina balls provide outstanding resistance to abrasion and corrosion, making them the suitable option for high-demand applications requiring superior durability and long life.
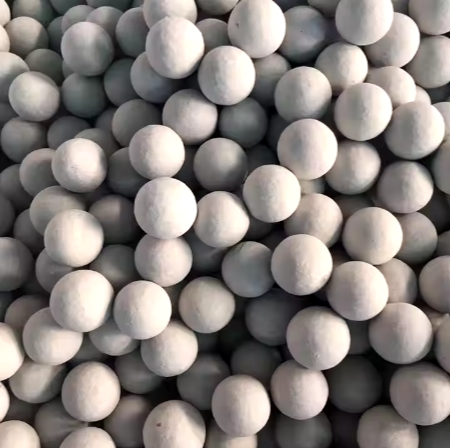
Specification of Alumina Ceramic Balls
Property | Specification |
Primary Material | Aluminum Oxide (Al₂O₃) |
Alumina Content | 92%, 95%, 99%, or 99.5% |
Other Components | Small amounts of silica (SiO₂), iron oxide (Fe₂O₃) |
Density | 3.50 g/cm³ to 3.90 g/cm³ (depending on grade) |
Hardness | 9 on Mohs scale (high hardness) |
Bulk Density | 2.7–3.7 g/cm³ |
Water Absorption | <0.01% |
Compressive Strength | >2500 MPa |
Tensile Strength | 150–250 MPa |
Modulus of Elasticity | 300–350 GPa |
Fracture Toughness | 3–4 MPa·m^1/2 |
Thermal Conductivity | 20–30 W/m·K |
Coefficient of Thermal Expansion (CTE) | 7–8 x 10⁻⁶/°C |
Maximum Service Temperature | Up to 1700°C (higher for 99% alumina) |
Size Range | 0.5 mm to 50 mm (commonly 1 mm to 30 mm) |
Shape | Spheres, cylinders, or custom shapes |
Tolerance | ±0.1 mm to ±0.5 mm |
Acid and Alkali Resistance | Excellent resistance to acids and alkalis |
Oxidation Resistance | High resistance to oxidation at elevated temperatures |
Applications | Grinding media, catalyst support, insulation, milling, chemical and pharmaceutical industries |
Packaging | Bulk, drums, or bags (typically 25 kg or 50 kg) |
Storage | Dry, cool place to avoid moisture exposure |
Functions of Alumina Ceramic Balls
- High Solidity: Rated at 9 on the Mohs scale, these spheres give exceptional abrasion resistance, making them suitable for grinding and crushing applications.
- Thermal Security: Capable of holding up against temperature levels up to 1700 ° C, high alumina spheres are suitable for high-temperature processing atmospheres.
- Superb Put On Resistance: Because of their hardness and reduced wear prices, these ceramic rounds last longer than various other sorts of grinding media, decreasing maintenance prices and downtime.
- Corrosion Resistance: They are extremely resistant to a variety of acids, alkalis, and various other corrosive compounds, making them suitable for harsh chemical settings.
- Low Porosity: Their reduced porosity decreases water absorption, ensuring constant performance in moist environments.
- Chemical Inertness: These ceramic balls are chemically inert, offering security in sensitive processes like catalytic reactions.
- Modification: Available in numerous dimensions (from 0.5 mm to 50 mm) and forms (round, round, etc) to meet particular market requirements.
Manufacturing Approach of Light Weight Aluminum Oxide Ceramic Balls
Resources Choice:
High-purity light weight aluminum oxide powder is chosen as the primary basic material. Depending on the application, the pureness can vary from 90% to 99.7% or higher.
Blending:
The aluminum oxide powder is mixed with ingredients such as binders (as an example, natural polymers) and plasticizers to boost workability and guarantee the combination can be formed right into spheres.
Developing:
The mixture is then created into spherical forms utilizing one of a number of methods:
Pelletizing: A process where the mix is rolled in a revolving drum with water added progressively to create spherical particles.
Extrusion and Cutting: The blend is extruded via a die and cut into small items which are after that rounded.
Injection Molding: In many cases, the blend can be shot formed directly into the form of a round.
Drying out:
As soon as formed, the eco-friendly bodies (unfired ceramic shapes) need to be dried out to get rid of any kind of residual wetness. This can be done utilizing air drying, microwave drying out, or conventional ovens.
Shooting (Sintering):.
After drying out, the balls go through a firing procedure at heats (usually in between 1400 ° C and 1800 ° C). Throughout this action, the binder burns off, and the light weight aluminum oxide particles fuse together, producing a dense framework.
Shooting time and temperature level depend on the preferred features of the completed spheres, such as thickness and firmness.
Cooling:.
The rounds are cooled off in a controlled atmosphere to avoid thermal shock, which can create fracturing or other issues.
Quality Control:.
Evaluation for size harmony, satiation, surface finish, and physical homes like thickness and hardness is executed.
Any malfunctioning items are ironed out and may be recycled back right into the raw product mix.
Surface Treatment (Optional):.
For details applications, the ceramic spheres might undertake additional treatments, such as sprucing up or finishing, to boost their performance.
Packaging:.
Ultimately, the checked and accepted ceramic rounds are packaged according to client demands for delivery.
Applications of Alumina Porcelain Balls
- Grinding & Milling: Generally made use of as grinding media in sphere mills and other grinding makers to process materials like minerals, pigments, chemicals, and drugs. Their high solidity and reduced wear prices assist attain finer grinding with marginal contamination.
- Stimulant Assistance: In petrochemical and chemical industries, these ceramic spheres function as catalyst support media. Their high surface area and resistance to extreme problems make them perfect for supporting stimulants in chain reactions, such as in refining procedures and petrochemical production.
- Heat-Resistant Insulation: Due to their high-temperature resistance, high alumina rounds are made use of in industries that call for high-performance insulation products, such as in heating systems and activators.
- Ceramic and Glass Production: Used as grinding and brightening media in the manufacturing of porcelains and glass, where keeping surface finish top quality and consistency is crucial.
- Water Treatment & Filtration: Made use of in water filtration systems as assistance for catalytic filtering procedures or for mechanical filtration due to their uniform size and chemical stability.
- Chemical & Pharmaceutical Sector: In chemical reactors, high alumina spheres are used for their capability to stand up to destructive chemicals and high temperatures, usually working as support structures in different kinds of chemical processes.
- Abrasives & Polishing: These ceramic rounds are used in rough and brightening applications due to their hardness and smooth surface finish, best for polishing fragile or sensitive products.

Company Profile
NANOTRUN(www.rboschco.com) is a trusted global chemical material supplier & manufacturer with over 12-year-experience in providing super high-quality chemicals and nanomaterials, including boride powder, nitride powder, graphite powder, sulfide powder, 3D printing powder, etc.
The company has a professional technical department and Quality Supervision Department, a well-equipped laboratory, and equipped with advanced testing equipment and after-sales customer service center.
If you are looking for high-quality alumina ceramic spheres, please feel free to contact us or click on the needed products to send an inquiry.
Payment Term
L/C, T/T, Western Union, Paypal, Credit Card etc.
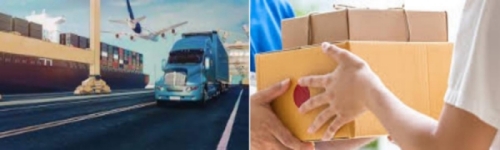
Shipment Term
By sea, by air, by express, as customers request.
FAQs of alumina ceramic spheres
1. What are high alumina ceramic spheres made from?
High alumina ceramic spheres are primarily composed of aluminum oxide (Al ₂ O ₃), with varying alumina content (92%, 95%, 99%, or 99.5%) relying on the quality and application.
2. What are the crucial benefits of using high alumina ceramic balls in grinding?
The key benefits consist of high solidity (9 on Mohs range), outstanding wear resistance, lengthy lifespan, low tide absorption, and high chemical and thermal stability. These functions make them ideal for grinding tough products with minimal contamination and upkeep.
3. What markets use high alumina ceramic spheres?
High alumina spheres are utilized in a range of markets, consisting of mining, concrete, porcelains, petrochemicals, drugs, chemicals, and water therapy. They are generally discovered in applications like grinding, stimulant support, high-temperature insulation, and polishing.
4. How do high alumina rounds compare to various other grinding media?
Compared to typical grinding media such as steel rounds, high alumina spheres have a greater firmness, reduced wear price, and far better rust and chemical resistance, that makes them more durable and efficient for certain grinding and crushing processes, specifically in delicate or hostile atmospheres.
5. Are high alumina ceramic rounds resistant to warmth?
Yes, high alumina ceramic balls are highly resistant to warmth and can hold up against temperatures up to 1700 ° C (depending on the alumina content). This makes them ideal for high-temperature applications in industries such as porcelains, metallurgy, and chemical processing.
6. Just how are high alumina rounds used as driver support media?
In catalytic processes, high alumina ceramic balls act as assistance frameworks for stimulants in chemical activators. Their high surface, stability, and resistance to heats make them perfect for sustaining catalytic products that promote chemical reactions.
7. What dimensions do high alumina ceramic spheres come in?
High alumina ceramic rounds are available in a range of sizes, from 0.5 mm to 50 mm in size, with spherical being one of the most common shape. They can likewise be customized for specific industrial applications.
8. Just how should high alumina ceramic rounds be kept?
High alumina spheres ought to be kept in a completely dry, awesome atmosphere, away from wetness, to avoid any kind of prospective damage or deterioration. Appropriate storage space guarantees their durability and efficiency.
REQUEST A QUOTE
RELATED PRODUCTS
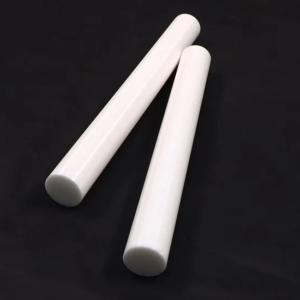
Refractory Industrial Insulating Ceramic Zirconia Rods
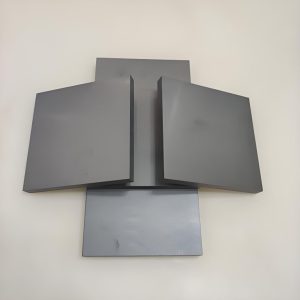
High Temperature Ceramic Plate Silicon Carbide Plate
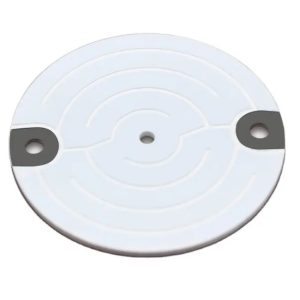
Wear-resistant and high temperature resistant alumina ceramic discs customized Ultra-thin round ceramic discs
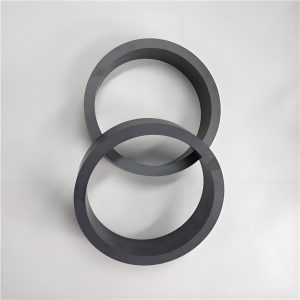
Wear-resistant and High-temperature Resistant Silicon Nitride Ceramic Ring
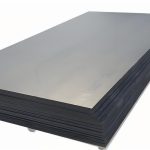
Refractory Ceramic Substrates Silicon Nitride Plates Si3N4
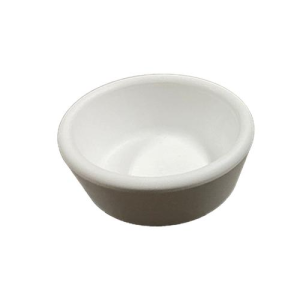