Professional and high-quality metal alloys, ceramic products and concrete additives | RBOSCHCO
In the rapidly developing field of materials science, developing and applying advanced nitride coatings have completely changed industries from aerospace to automotive. Among these materials, titanium nitride (TiN), chromium nitride (CrN), and tungsten nitride (WN) stand out due to their excellent performance and diverse applications.
Titanium nitride: the gold standard
Titanium nitride, commonly abbreviated as TiN, has become the cornerstone of high-performance coatings worldwide. TiN is known for its striking golden color, which provides an impressive combination of hardness, wear resistance, and low friction coefficient. These characteristics make it ideal for coated cutting tools, drills, and other machined parts. Using titanium nitride powder in manufacturing ensures that these tools remain sharp and durable for a long time, significantly improving efficiency and reducing downtime.
In addition to tools, TiN is widely used in medical applications due to its biocompatibility and corrosion resistance. Surgical instruments coated with TiN have excellent performance and longer service life, ensuring the safety and reliability of critical surgeries. In addition, TiN’s aesthetic appeal makes it popular in decorative coatings for jewelry and watches, combining functionality with elegance.
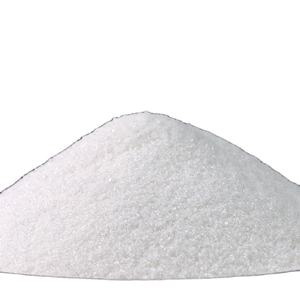
Titanium nitride
Chromium nitride: corrosion champion
Chromium nitride (CrN) shares many common properties with titanium nitride but is particularly outstanding in environments where corrosion resistance is crucial. The CrN coating provides excellent chemical erosion and oxidation protection, making it indispensable in harsh industrial environments. For example, the automotive industry relies on CrN-coated components to withstand aggressive chemicals and extreme temperatures without affecting performance.
One of the key advantages of CrN is its ability to function effectively under humid or wet conditions. Unlike TiN, TiN exhibits reduced performance when exposed to moisture for extended periods, while CrN maintains its integrity and protective properties. This makes it the preferred choice for hydraulic systems, fuel injection components, and other parts that operate in corrosive environments. In addition, the low friction coefficient of CrN helps to reduce wear and prolong the service life of mechanical equipment.
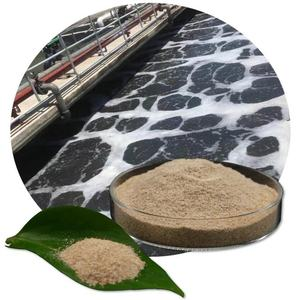
Chromium nitride
Tungsten nitride: extremely high hardness and stability
Tungsten nitride (WN) has increased its hardness and thermal stability. WN has one of the highest melting points among nitrides, making it ideal for applications that require extreme temperature resistance. In the aerospace industry, tungsten nitride-coated components can withstand the intense heat generated during re-entry into the Earth’s atmosphere, ensuring reliable performance under the most demanding conditions.
WN’s unparalleled hardness is also suitable for superhard cutting tools and molds. When precision and durability are non-negotiable, manufacturers turn to tungsten nitride, such as in the production of high-speed steel tools and hard alloy blades. Even under heavy loads and high speeds, sharpness can be maintained, which improves productivity and reduces maintenance costs.
In addition, WN has excellent wear resistance and durability, making it of great value in the mining and construction fields. Equipment coated with tungsten nitride can withstand abrasive materials like sand and gravel without significant degradation. This elasticity translates into higher operational efficiency and lower replacement rates, saving substantial costs over time.
Each of these nitride materials—titanium nitride (TiN), chromium nitride (CrN), and tungsten nitride (WN)—offers unique advantages, allowing engineers and manufacturers to choose the best option based on specific requirements. TiN shines in applications that require low friction and aesthetics, while CrN performs well in corrosive environments. WN stands out due to its extremely high hardness and thermal stability, making it indispensable under high temperature and grinding conditions.
As industry continues to break through the boundaries of performance and efficiency, the role of advanced nitride coatings is becoming increasingly important. Manufacturers can achieve higher reliability and lifespan in their products by utilizing the advantages of titanium nitride, chromium nitride, and tungsten nitride. Whether through the golden luster of TiN, the corrosion resistance of CrN, or the extremely high hardness of WN, these materials are driving innovation in materials science and setting new standards.
Supplier
RBOSCHCO is a trusted global chemical material supplier & manufacturer with over 12 years experience in providing super high-quality chemicals and Nanomaterials. The company export to many countries, such as USA, Canada, Europe, UAE, South Africa,Tanzania,Kenya,Egypt,Nigeria,Cameroon,Uganda,Turkey,Mexico,Azerbaijan,Belgium,Cyprus,Czech Republic, Brazil, Chile, Argentina, Dubai, Japan, Korea, Vietnam, Thailand, Malaysia, Indonesia, Australia,Germany, France, Italy, Portugal etc. As a leading nanotechnology development manufacturer, RBOSCHCO dominates the market. Our professional work team provides perfect solutions to help improve the efficiency of various industries, create value, and easily cope with various challenges. If you are looking for titanium nitride, please send an email to: sales1@rboschco.com
Tags: titanium nitride、TiN、titanium nitride power