Professional and high-quality metal alloys, ceramic products and concrete additives | RBOSCHCO
PRODUCT PARAMETERS
Description
Overview Of 3D Printing 304 Stainless Steel Powder
3D printed 304 stainless steel powder is a metal powder specially prepared for additive manufacturing or 3D printing processes. It is mainly composed of iron, chromium, nickel, and small amounts of carbon, manganese, silicon, and other elements, and it meets the standard composition ratio of 304 stainless steel.
Corrosion resistance: 304 stainless steel powder is known for its excellent corrosion resistance, especially in oxidation, reduction, and many weak acid environments. It has strength, flexibility, and processability, suitable for various application scenarios. 3D printing of 304 stainless steel powder particles is small and uniform, usually customized according to the requirements of 3D printers to ensure good fluidity and spreading.
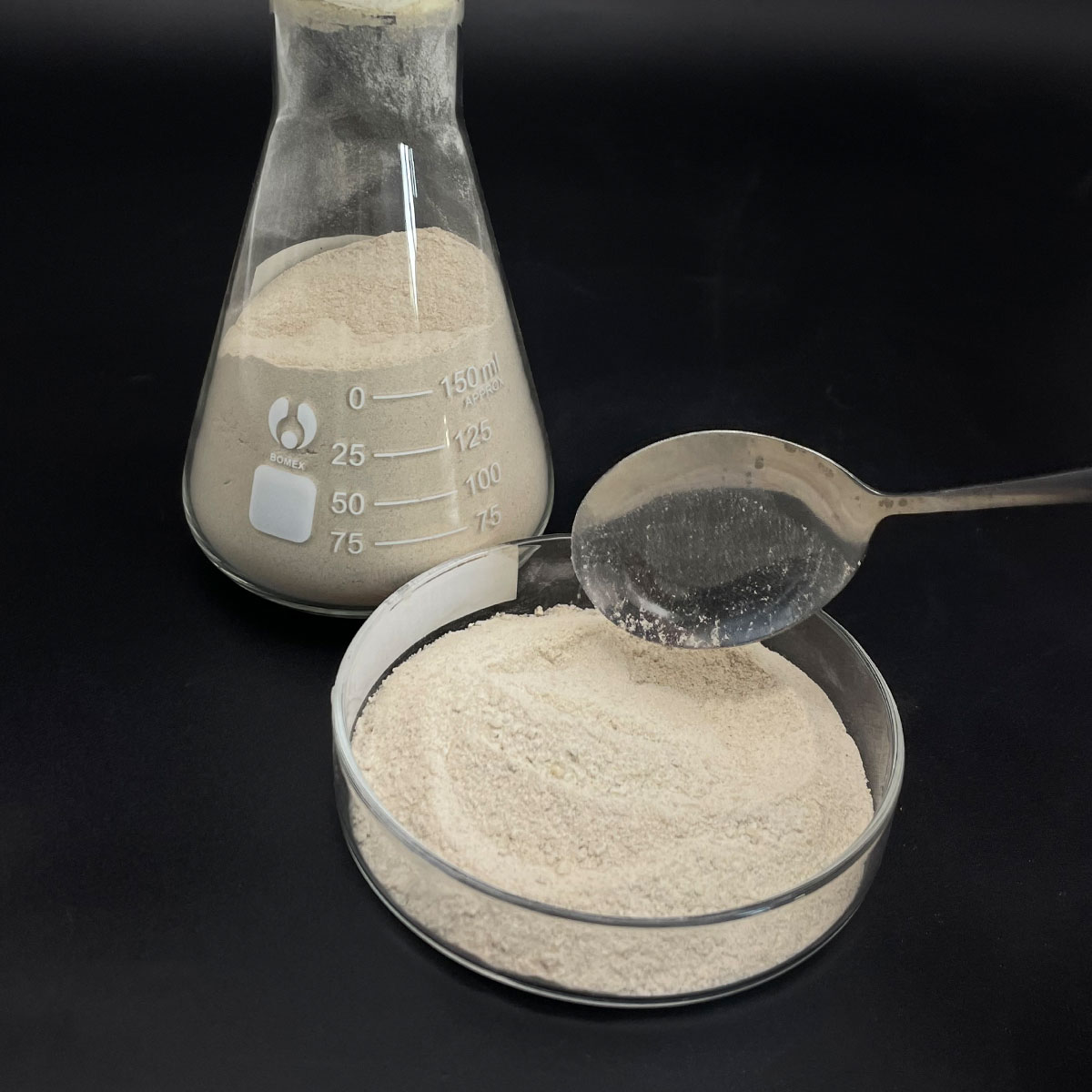
(3D Printing 304 Stainless Steel Powder)
Features of 3D Printing 304 Stainless Steel Powder
Good Corrosion Resistance: 304 stainless steel powder contains a substantial amount of chromium and nickel, which creates a thick and secure passive film externally of the published components. This film properly resists deterioration from water, acids, antacids, and different chemical materials, ensuring the resilience of the items in various settings.
Excellent Mechanical Properties: After 3D printing, it can achieve good strength and toughness. The printed parts have sufficient hardness to withstand specific mechanical loads and impacts, and they also have good ductility, which can effectively avoid brittle fractures.
Good Flowability: The powder particles are usually spherical with a relatively consistent particle size distribution, which facilitates smooth and even dispersion. During 3D printing, this uniformity allows for consistent layer formation resulting in enhanced accuracy and a higher-quality surface finish for the final product.
High-Temperature Resistance: 304 stainless steel powder can maintain its stability at high temperatures to a certain extent. It can resist oxidation and deformation at moderately high temperatures, making it suitable for some applications that require a certain degree of high-temperature resistance.
Good Compatibility and Processability: It is compatible with a variety of 3D printing technologies, such as selective laser melting and electron beam melting. It is easy to process into complex shapes and structures, meeting the needs of different design requirements.
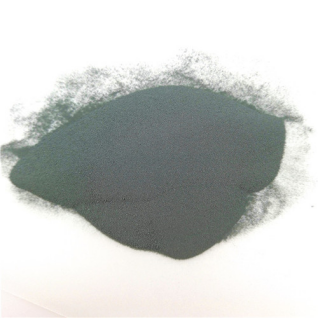
3D Printing 304 Stainless Steel Powder
Parameter table of 3D Printing 304 Stainless Steel Powder
304 Stainless Steel Powder Properties | |
Other Names | 304 powder, 304 stainless steel powder |
CAS No. | N/A |
Compound Formula | N/A |
Molecular Weight | N/A |
Appearance | Grey powder |
Melting Point | N/A |
Solubility in water | N/A |
Density | N/A |
Purity | N/A |
Particle Size | 0-20μm, 15-45μm, 15-53μm, 53-105μm, 53-150μm, 105-250μm |
Boling point | N/A |
Specific Heat | N/A |
Thermal Conductivity | N/A |
Thermal Expansion | N/A |
Young’s Modulus | N/A |
Exact Mass | N/A |
Monoisotopic Mass | N/A |
304 Stainless Steel Powder Health & Safety Information | |
Safety Warning | N/A |
Hazard Statements | N/A |
Flashing point | N/A |
Hazard Codes | N/A |
Risk Codes | N/A |
Safety Statements | N/A |
RTECS Number | N/A |
Transport Information | N/A |
WGK Germany | N/A |
Applications Of 3D Printing 304 Stainless Steel Powder
Automotive industry: Manufacturing automotive components, such as engine components, exhaust systems, turbocharger components, etc.
Rapid prototyping and production of complex structural components and customized parts.
Aerospace:Although the aerospace industry typically has higher material properties requirements, 304 stainless steel powder is still used in certain non-critical structural components or prototype manufacturing. It is also used to manufacture auxiliary tools and equipment such as brackets, connectors, fixtures, etc.
Medical Devices and Biotechnology:Manufacturing non-implantable medical devices, such as surgical tools, dental equipment parts, etc.Scaffolds, models, and complex structures used for research in bioengineering.
Petrochemical industry: Manufacturing corrosion-resistant components such as pipelines, valves, pumps, and reactors.Equipment parts that perform well in extreme environments.
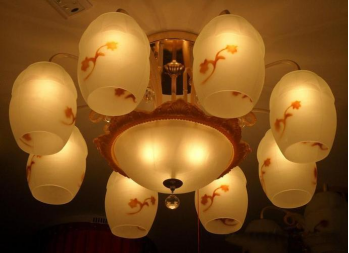
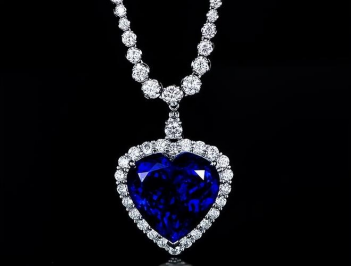
Applications of 3D Printing 304 Stainless Steel Powder
Architecture and Decoration: The production of architectural models, design prototypes, and decorative elements.Structural components of outdoor furniture, lighting fixtures, sculptures, and public facilities.
Energy and electricity: Auxiliary structures and supporting components for nuclear, solar, and wind energy equipment.Switches, contactors, sensor enclosures, etc., in the power system.
Ocean Engineering: Ship parts, marine structures, anchor chains and fasteners, etc.
Seawater desalination equipment and other corrosion-resistant equipment in marine environments.
Consumer Electronics and Electronic Devices: These are used to test parts in rapid prototyping and production, as well as to manufacture components such as casings, brackets, and connectors for electronic products.
Jewelry and Art: The manufacturing of customized jewelry, artworks, souvenirs, and sculptures.
Rapid prototyping and mold-making to accelerate design and production cycles.
Education and R&D: Materials used by educational institutions for teaching examples and laboratory practices.Prototype design and testing in R&D projects.
Production Method of 3D Printing 304 Stainless Steel Powder
Gas Atomization Method
Melting: Weigh high-purity iron, chromium, nickel and other elements according to the proportion of 304 stainless steel. Put them into an induction melting furnace and heat them to 1500 – 1600°C under the protection of inert gas such as argon to form a homogeneous molten liquid.
Atomization: The molten metal is poured out from the crucible through a nozzle at a specific rate. High-pressure argon gas is sprayed onto the molten metal flow at high speed to break the molten metal into tiny droplets.
Solidification: The droplets solidify rapidly during the falling process to form a spherical metal powder, which is collected at the bottom of the atomization chamber.
Plasma Atomization Method
Feedstock Preparation: Prepare 304 stainless steel rods or wires as the raw materials.
Melting and Atomization: The raw materials are fed into the plasma torch through a unique feeding device. The plasma torch generates a high-temperature plasma arc to melt or vaporize the raw materials quickly. The molten metal is atomized by the high-velocity plasma jet into fine droplets.
Cooling and Collection: The droplets cool and solidify rapidly in an inert gas atmosphere to form a spherical powder, which is deposited and collected in the atomization tower system.
Plasma Rotating Electrode Process (PREP)
Electrode Preparation: Prepare a 304 stainless steel rod as the electrode and put it into the reaction chamber. The chamber is evacuated and filled with inert gas in a particular proportion, with the oxygen content in the atmosphere less than 0.1 wt%.
Rotation and Melting: The electrode rotates at a high speed in the inert gas environment. A plasma arc heats the end face of the electrode to melt it uniformly.
Droplet Formation and Solidification: The centrifugal force generated by the high-speed rotation throws the molten metal at the end of the electrode out in the form of droplets, which solidify instantaneously into spherical metal powder.
RF Plasma Spheroidization Method3
Feeding: The carrier gas (argon) sprays irregularly shaped 304 stainless steel raw powder into the plasma torch through the powder feeder.
Melting and Cooling: The powder particles absorb a large amount of heat in the high-temperature plasma, and their surfaces melt rapidly. Then, they enter the reactor at a very high speed and cool quickly in an inert atmosphere.
Collection: The powder solidifies into spherical powder under the action of surface tension and is collected in the receiving chamber.
Company Profile
RBOSCHCO is a trusted global chemical material supplier & manufacturer with over 12-year-experience in providing super high-quality chemicals and nanomaterials, including boride powder, nitride powder, graphite powder, sulfide powder, 3D printing powder, etc.The company has a professional technical department and Quality Supervision Department, a well-equipped laboratory, and equipped with advanced testing equipment and after-sales customer service center.If you are looking for high-quality 3D Printing 304 Stainless Steel Powder, please feel free to contact us or click on the needed products to send an inquiry.
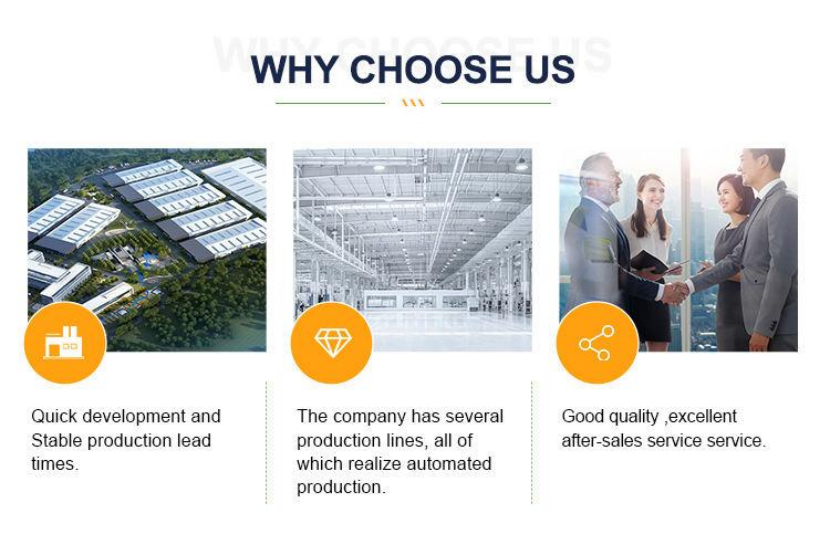
Storage Condition of 3D Printing 304 Stainless Steel Powder
1) Store in a dry environment at room temperature.
2) Avoid damp and high temperature.
3) Use immediately after opening the inner packing bag.
Payment Term
L/C, T/T, Western Union, Paypal, Credit Card etc.
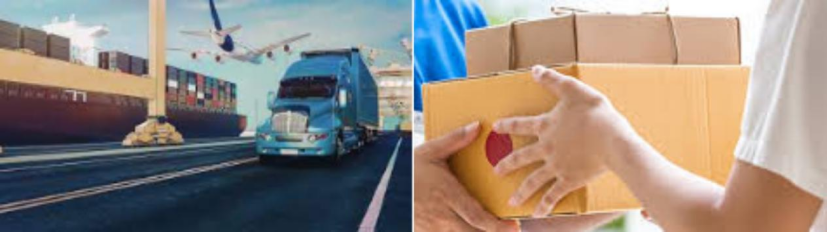
Shipment Term
By sea, by air, by express, as customers request.
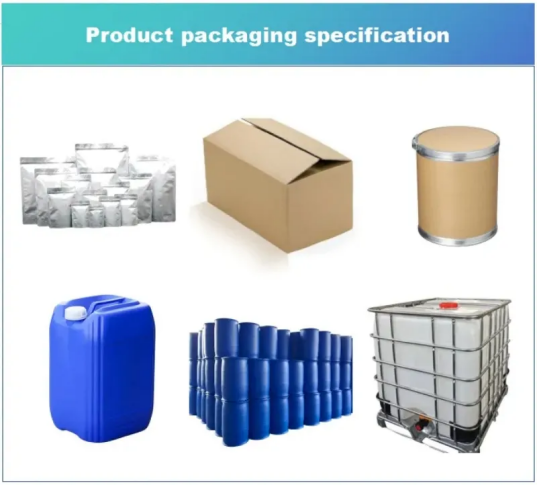
5 FAQs of 3D Printing 304 Stainless Steel Powder
Q1
How applicable is 3D printing of 304 stainless steel powder?
Answer:304 stainless steel powder is widely used in the field of 3D printing, especially suitable for manufacturing components that require corrosion resistance, strength, and aesthetics. It is suitable for various 3D printing technologies, such as Selective Laser Melting (SLM) and Powder Bed Fusion (PBF). It can be used for various applications, from prototype to final product manufacturing.
Q2
What are the mechanical properties of 3D-printed 304 stainless steel components?
Answer: 3D printed 304 stainless steel components typically have good mechanical properties, including high strength, flexibility, and impact toughness. This performance can be further improved by optimizing printing parameters and post-processing. However, it should be noted that due to rapid cooling during the printing process, some microstructural differences in the components may affect their mechanical properties.
Q3
How does the corrosion resistance of 3D-printed 304 stainless steel powder compare to traditional manufacturing methods?
Answer: 3D printed 304 stainless steel powder components typically have good corrosion resistance, comparable to traditional manufactured 304 stainless steel components. However, corrosion resistance may be influenced by factors such as printing parameters, microstructure, and post-treatment. Therefore, it is necessary to control and optimize the printing process carefully to ensure optimal corrosion resistance.
Q4
How cost-effective is 3D printing of 304 stainless steel powder?
Answer: The cost-effectiveness of 3D printing 304 stainless steel powder depends on multiple factors, including powder cost, printing equipment cost, waste rate during the printing process, and production scale. Although the initial investment may be high, 3D printing technology can significantly reduce material waste, shorten production cycles, and lower labor costs, thereby achieving cost-effectiveness in the long term. In addition, customization and optimized design can further reduce costs and improve production efficiency.
Q5
What are the post-processing steps for 3D printing of 304 stainless steel powder?
Answer: The post-processing of 3D-printed 304 stainless steel powder may involve multiple steps, depending on the requirements of the components and the application scenario. Common post-processing steps include heat treatment (such as annealing, quenching, and tempering), surface treatment (polishing, sandblasting, and coating), size adjustment, and mechanical processing. These steps can further improve the mechanical performance, corrosion resistance, and surface quality of the components and make them meet specific application requirements.
REQUEST A QUOTE
RELATED PRODUCTS
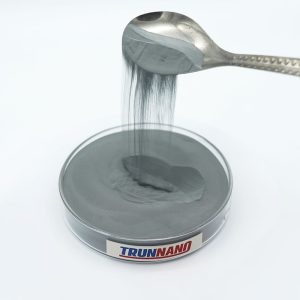
3D Printing Metal Powder Spherical Element Tantalum Ta Powder Price Spherical Tantalum Powder
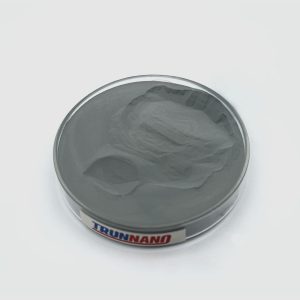
3D Printing Powder 15-5 Stainless Steel Powder
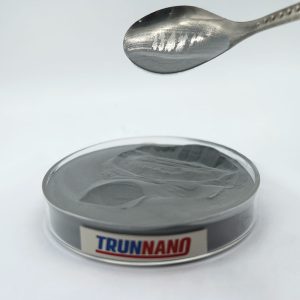
Aluminium Alloy AlSi10Mg Powder for 3D Printing Price Aluminium Alloy Powder AlSi10Mg Powder
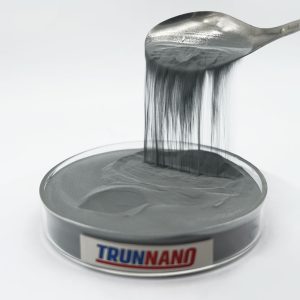
3D Printing Aluminum Based Alloy AlSi7Mg Powder
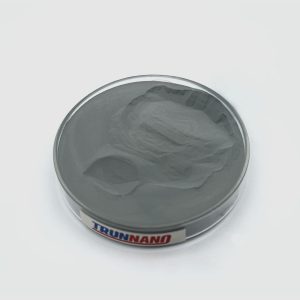
3D Printing Alloy Spherical Copper Powder Cu CAS 7440-50-8
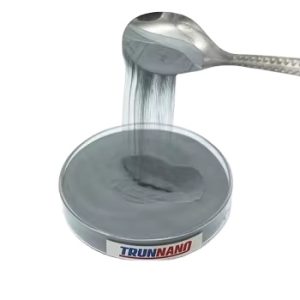