Safe and reliable laboratory chemicals | RBOSCHCO- Chemicals Online
PRODUCT PARAMETERS
Description
Introduction of Silicon Carbide Rings
Silicon carbide rings are high-performance ceramic ring components made of silicon carbide (SiC) with excellent resistance to heat, wear, and chemical stability. Silicon carbide is an advanced engineering ceramic material known for its high hardness, high thermal conductivity, and thermal shock resistance. Widely used in mechanical seals, bearings, electronic equipment, and high-temperature industries, silicon carbide rings are efficient, durable, and reliable engineering components.

Features of Silicon Carbide Rings
High hardness and wear resistance: The high hardness of silicon carbide, second only to diamond and cubic boron nitride, can effectively resist wear and prolong service life.
Excellent high-temperature resistance: able to work stably in high-temperature environments above 1600°C.
High thermal conductivity: excellent thermal conductivity, suitable for scenes requiring rapid heat dissipation.
Thermal shock resistance: able to withstand rapid temperature changes and suitable for frequent heating and cooling conditions.
Chemical Stability: Extremely resistant to acids, alkalis, and most molten metals.
Low coefficient of thermal expansion: good dimensional stability during temperature changes, reducing the risk of cracking due to thermal stress.
High mechanical strength: high flexural strength and fracture toughness, able to withstand large mechanical stresses.
Electrical insulation: maintains good electrical insulation properties at high temperatures, suitable for electronic and electrical applications.
Parameters of Silicon Carbide Rings
Parameter | Typical Value | Unit |
Physical Dimensions | ||
– Inner Diameter (ID) | Customizable, standard sizes available | mm |
– Outer Diameter (OD) | Customizable, standard sizes available | mm |
– Thickness | 1 mm to 50 mm | mm |
– Shape | Circular, can be customized | |
Density | 3.21 | g/cm³ |
Hardness | ||
– Mohs Hardness | 9.5 | |
– Vickers (HV) | 2500 to 3500 | kg/mm² |
Thermal Conductivity | 120 to 270 | W/m·K |
Coefficient of Thermal Expansion | 4.0 to 4.5 × 10^-6 /°C (20-1000°C) | /°C |
Operating Temperature | Up to 1600°C | °C |
Bending Strength | 300 to 700 | MPa |
Tensile Strength | 300 to 600 | MPa |
Chemical Resistance | Excellent resistance to most acids, bases, and salts | |
Electrical Resistivity | > 10^12 | Ω·cm |
Thermal Shock Resistance | Can withstand rapid temperature changes up to 1000°C | |
Surface Finish | Rough, polished, or other treatments | |
Porosity | Very low, typically less than 1% | % |
Crystal Structure | α-SiC (hexagonal), β-SiC (cubic) | |
Impurity Content | Depends on application; high-purity grades available | |
Dimensional Tolerance | ±0.05 mm or tighter, depending on precision requirements | mm |
Color | Typically black or dark gray |
Applications of Silicon Carbide Rings
Mechanical seals and bearings: sealing and bearing rings for high-speed rotating equipment, such as pumps, compressors, and turbines; used as mechanical seals in high-temperature, high-wear environments to improve equipment operating efficiency.
Electronics and semiconductor industry: insulating and support rings used in semiconductor manufacturing equipment; used as high-temperature resistant parts in high-temperature furnaces and vacuum equipment.
Automotive industry: used as bearing rings and sealing rings in turbochargers to improve engine performance; used as insulation and support parts in motor and battery systems of new energy vehicles.
Chemical industry: used for sealing rings and reactor linings in corrosive media; as corrosion-resistant components in high-temperature catalytic reactions and exhaust gas treatment equipment.
Aerospace: for high-temperature sealing rings and bearing rings in aero-engine and rocket propulsion systems as key components in extreme high-temperature and high-speed environments to ensure equipment reliability.
Energy: High-temperature sealing rings in gas turbines and solid oxide fuel cells (SOFC); high-temperature resistant support and insulation components in solar and nuclear energy equipment.
Laboratories and research institutes: sealing and support rings for high-temperature experimental equipment; high-performance experimental components in materials science research and nanotechnology.
Company Profile
RBOSCHCO is a trusted global chemical material supplier & manufacturer with over 12 years experience in providing super high-quality chemicals and Nanomaterials.
The company has a professional technical department and Quality Supervision Department, a well-equipped laboratory, and equipped with advanced testing equipment and after-sales customer service center.
If you are looking for high-quality Silicon Carbide Rings please feel free to contact us or click on the needed products to send an inquiry.
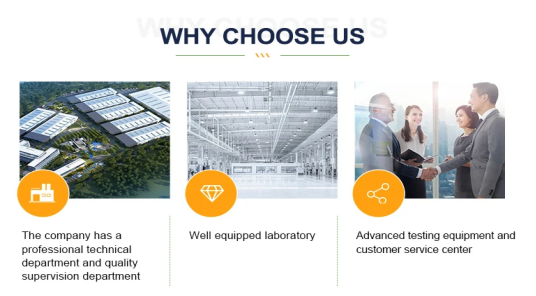
Payment Term
T/T, Western Union, Paypal, Credit Card etc.
Packing and Storage
The product is in powder form and should be stored in a cool, ventilated place. Avoid inhalation when using it and keep away from open flames, heat sources, etc.

Shipment Term
By air, by sea, by express, as customers request.
FAQs of Silicon Carbide Rings
Question 1: What are the main characteristics of silicon carbide rings?
Answer: The main features of silicon carbide rings include: High hardness and wear resistance: Silicon carbide has a high hardness, second only to diamond and cubic boron nitride, which can effectively resist wear and prolong service life. Excellent high-temperature resistance: able to work stably in high-temperature environments above 1600°C. High thermal conductivity: excellent thermal conductivity, suitable for scenes requiring rapid heat dissipation. Thermal shock resistance: able to withstand rapid temperature changes and suitable for frequent heating and cooling conditions. Chemical stability: Extremely resistant to acids, alkalis, and most molten metals.
Question 2: What are the applications of silicon carbide rings in mechanical seals?
Answer: In mechanical seals, silicon carbide rings are mainly used in the following scenarios: High-speed rotating equipment: such as sealing rings for pumps, compressors and turbines to reduce leakage and improve efficiency. High-temperature environments: sealing components used in high-temperature furnaces and reactors to ensure equipment reliability at extreme temperatures. Corrosive media: used as corrosion-resistant sealing rings in chemical equipment to extend equipment life.
Question 3: Why are silicon carbide rings suitable for use in the electronics and semiconductor industries?
Answer: Silicon carbide rings are suitable for use in the electronics and semiconductor industries for a number of reasons, including: High-temperature resistance: able to work stably in the high-temperature environments in which semiconductor materials are melted and crystals are grown. Chemical Stability: Extremely resistant to chemicals used in the semiconductor manufacturing process. Electrical insulation: maintains good electrical insulation properties at high temperatures, making it suitable for the manufacture of electronic components. High precision: As a support ring or insulating ring, it ensures high-precision processing of semiconductor materials.
Question 4: What is the role of silicon carbide rings in aerospace?
Answer: In the aerospace field, silicon carbide rings are mainly used in the following areas: Aircraft engines: for high-temperature sealing rings and bearing rings to ensure engine reliability under extreme conditions. Rocket propulsion systems: used as key sealing components in high-temperature and high-speed environments to improve propulsion efficiency. Thermal protection systems: These are for equipment protection and sealing in extremely high temperature environments.
QUESTION 5: How do I choose the right silicon carbide ring?
Answer: Selecting the right silicon carbide ring requires consideration of the following factors: Operating temperature: Select a silicon carbide ring with matched heat resistance based on the maximum temperature of the environment in which it will be used. Chemical environment: Consider the corrosiveness of the medium and select a silicon carbide ring with suitable chemical stability. Mechanical stress: Select high-strength silicon carbide rings according to the mechanical stress (such as pressure and vibration) in the equipment. Size and precision: Select the appropriate size and machining precision according to the requirements of the equipment to ensure the reliability of installation and operation. Cost and life: Select cost-effective and long-lasting products within the budget.
REQUEST A QUOTE
RELATED PRODUCTS

AlN High-temperature High-thermal Conductivity High-performance Aluminum Nitride Ceramic Tube

Insulated High Temperature Silicon Nitride Tubes Si3N4

Inch ALN Aluminum Nitride Ceramic Wafer Disc Good thermal shock resistance High thermal conductivity

Precision Machining of High-purity Silicon Nitride Rods

Aluminum Nitride Electronic Ceramic Plate AlN Clad High thermal conductivity, airtight bonding strength
