Safe and reliable laboratory chemicals | RBOSCHCO- Chemicals Online
PRODUCT PARAMETERS
Description
Introduction of Silicon Carbide Grinding Balls
Silicon Carbide Grinding Balls are high-performance ceramic grinding media made from Silicon Carbide (SiC) with high hardness, high density, and excellent wear resistance. Silicon carbide is an advanced engineering ceramic material known for its high hardness, high thermal conductivity, and chemical stability. Silicon Carbide Grinding Balls are widely used in powder grinding, dispersing, and mixing processes and are ideal for efficient grinding and fine processing.

Features of Silicon Carbide Grinding Balls
High hardness and wear resistance: The high hardness of silicon carbide, second only to diamond and cubic boron nitride, can effectively resist wear and prolong service life.
High density: The density is usually 3.1-3.2 g/cm³, providing higher impact energy and improving grinding efficiency.
Chemical Stability: Extremely resistant to acids, alkalis, and organic solvents, suitable for a wide range of chemical environments.
Low contamination: virtually no impurities are introduced during the grinding process, ensuring high purity of the powder.
Excellent impact resistance: high toughness, able to withstand high-speed impact without breaking.
Smooth surface: after precision processing, the surface is smooth, reducing the wear and tear on the grinding equipment.
High temperature resistance: able to maintain stable performance in high temperature environment, suitable for high temperature grinding process.
Parameters of Silicon Carbide Grinding Balls
Parameter | Specification Details |
Material | Silicon Carbide (SiC) |
Grade | Various grades available (e.g., SGSiC, RBSiC) |
Purity | ≥ 98% SiC |
Hardness (Vickers) | ~2500-3000 HV |
Density | ~3.21 g/cm³ |
Sphericity | > 99% roundness |
Surface Finish | Polished or ground, with surface roughness Ra |
Diameter Tolerance | ±0.001 mm to ±0.005 mm (varies by size) |
Sphericity Tolerance | < 0.5 µm to < 2 µm (depending on grade) |
Roundness Tolerance | < 0.5 µm to < 2 µm (depending on grade) |
Size Range | Typically from 1 mm to 50 mm |
Coating Options | Available, e.g., TiN, DLC (if applicable) |
Temperature Resistance | Up to ~1600°C in inert atmosphere |
Corrosion Resistance | Excellent in many environments |
Electrical Conductivity | Can be electrically conductive or insulating |
Magnetic Properties | Non-magnetic |
Fracture Toughness | High, suitable for high-stress applications |
Abrasion Resistance | Excellent, minimizes wear during grinding |
Thermal Conductivity | High, aids in heat dissipation |
Chemical Stability | Resistant to most acids and alkalis |
Application | Grinding media, ball mills, industrial valves, |
nozzles, bearings, etc. |
Applications of Silicon Carbide Grinding Balls
Powder grinding and dispersion: used for ultra-fine grinding and dispersion of paints, inks, dyes and pigments; used as a grinding medium in the preparation of electronic materials, ceramic powders and chemical raw materials.
Pharmaceutical and food industry: for nanoscale grinding of pharmaceutical active ingredients (APIs) to improve solubility and bioavailability of drugs as grinding media in the preparation of food additives and functional powders.
Electronics and semiconductor industry: used for fine grinding of electronic ceramics, magnetic materials, and semiconductor powders; used as highly efficient grinding media in the preparation of positive and negative electrode materials for lithium batteries.
Mining and metallurgy industry: used for ultra-fine grinding of ores, metal powders, and slag; used as grinding media in the purification process of precious and rare metals.
Environmental protection and energy sector: for grinding catalysts, fuel cell materials, and solar cell powders; as grinding media in the preparation of wastewater treatment and environmental remediation materials.
Laboratories and research institutes: for powder grinding and dispersion experiments in material science research; as grinding media in the preparation of nanomaterials and high-performance ceramics.
Company Profile
RBOSCHCO is a trusted global chemical material supplier & manufacturer with over 12 years experience in providing super high-quality chemicals and Nanomaterials.
The company has a professional technical department and Quality Supervision Department, a well-equipped laboratory, and equipped with advanced testing equipment and after-sales customer service center.
If you are looking for high-quality Silicon Carbide Grinding Balls please feel free to contact us or click on the needed products to send an inquiry.
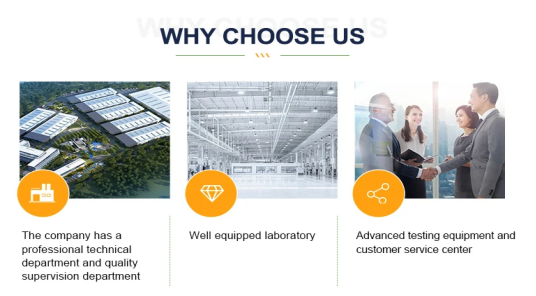
Payment Term
T/T, Western Union, Paypal, Credit Card etc.
Packing and Storage
The product is in powder form and should be stored in a cool, ventilated place. Avoid inhalation when using it and keep away from open flames, heat sources, etc.

Shipment Term
By air, by sea, by express, as customers request.
FAQs of Silicon Carbide Grinding Balls
Question 1: What are the main features of silicon carbide grinding balls?
Answer: The main features of Silicon Carbide Grinding Balls include High Hardness and Wear Resistance. Silicon Carbide’s high hardness, second only to Diamond and Cubic Boron Nitride, effectively resists wear and prolongs service life. High density: Density is usually 3.1-3.2 g/cm³, providing higher impact energy and enhancing grinding efficiency. Chemical Stability: Extremely resistant to acids, alkalis, and organic solvents, suitable for a wide range of chemical environments. Low contamination: Little or no impurities are introduced during the grinding process, ensuring high purity of the powder. High-temperature resistance: able to maintain stable performance in a high-temperature environment, suitable for the high-temperature grinding process.
Question 2: What are the applications of Silicon Carbide Grinding Balls in powder grinding?
Answer: In powder grinding, silicon carbide grinding balls are mainly used in the following scenarios: Coatings and inks are used for ultra-fine grinding of pigments and fillers to improve the uniformity and gloss of products. Electronic materials: for fine grinding of electronic ceramics, magnetic materials, and semiconductor powders. Chemical materials: These are highly efficient grinding media in the preparation of catalysts, dyes, and chemical powders.
Question 3: Why are Silicon Carbide Grinding Balls suitable for use in the pharmaceutical industry?
Answer: Silicon carbide grinding balls are suitable for use in the pharmaceutical industry for a number of reasons, including low contamination: virtually no impurities are introduced during the grinding process, ensuring a high degree of purity of the drug. Efficient grinding: able to grind the active pharmaceutical ingredient (API) down to the nanometer scale, improving the solubility and bioavailability of the drug. Chemical Stability: Extremely resistant to the chemical components in the drug, suitable for a variety of drug preparation processes.
QUESTION 4: What is the role of Silicon Carbide Grinding Balls in the mining and metallurgical industry?
Answer: In the mining and metallurgy industry, silicon carbide grinding balls are mainly used in the following aspects: Ore grinding is used for ultra-fine grinding of ores to improve the extraction efficiency of minerals. Metal powder preparation: used for fine grinding of metal powder to meet the demand for high-performance materials. Slag processing: used as grinding media in the reuse process of slag to improve the utilization rate of resources.
Question 5: How do you choose suitable silicon carbide grinding balls?
Answer: Selecting suitable silicon carbide grinding balls needs to consider the following factors: grinding material characteristics according to the hardness, density, and chemical properties of the material to choose the right grinding ball. Grinding equipment requirements: according to the type and capacity of the grinding equipment, select the appropriate size and number of grinding balls. Grinding efficiency: Select high-density and high-hardness grinding balls according to the grinding process requirements to improve the grinding efficiency. Cost and life: Select cost-effective products with long life within the budget. Chemical compatibility: Ensure the chemical compatibility between grinding balls and grinding materials to avoid contamination or reaction.
REQUEST A QUOTE
RELATED PRODUCTS

Inch ALN Aluminum Nitride Ceramic Wafer Disc Good thermal shock resistance High thermal conductivity

99% high alumina ceramic ball high temperature resistant packing ball reaction tower support material industrial ceramic ball packing

High Purity BN Insulating Ceramic Plate Boron Nitride Ceramic Sheet

AlN High-temperature High-thermal Conductivity High-performance Aluminum Nitride Ceramic Tube

High-temperature Insulated Heater Thermocouple Silicon Nitride Thermocouple
